Choosing the right materials is essential for product durability and customer satisfaction. Start by defining your product requirements based on functionality, intended use, and target audience preferences. Evaluate materials based on performance, cost, and environmental factors, while also considering the manufacturing process. Collaborate with suppliers for insights and engage in thorough testing of prototypes. This approach helps in making informed decisions. Keep exploring to uncover the best options tailored to your needs.
Key Takeaways
- Assess the environmental conditions your product will face to ensure material suitability and durability.
- Define your product requirements by considering user preferences, functionality, and aesthetics to guide material selection.
- Evaluate mechanical and chemical properties of materials to ensure they meet performance and regulatory standards.
- Collaborate with material suppliers and manufacturing partners for insights that enhance material choices and sourcing options.
- Conduct thorough testing and prototyping to validate material performance under intended use conditions before final selection.
Understanding the Importance of Material Selection
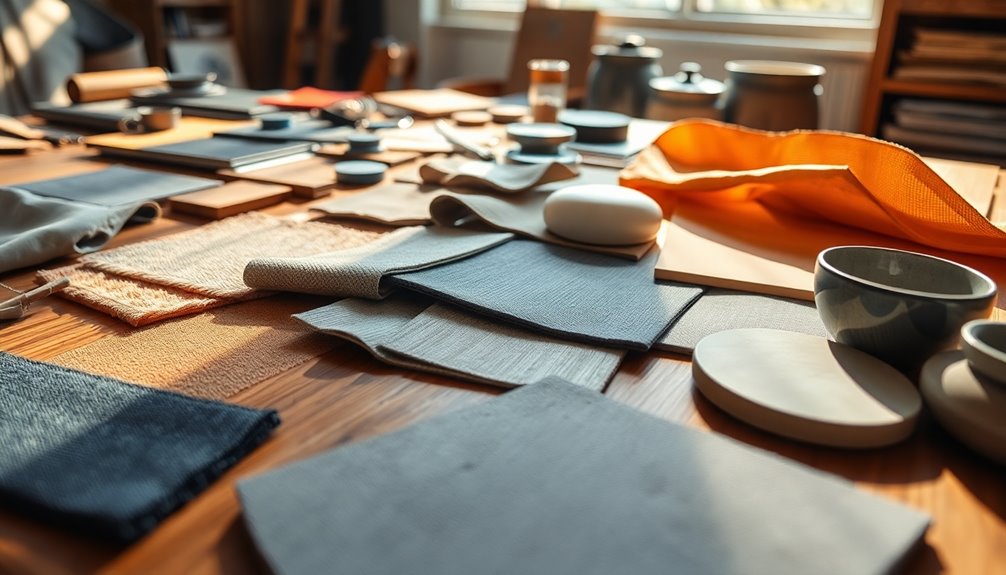
When you choose materials for your products, you're not just making a simple decision; you're setting the stage for their performance and longevity.
The material selection process is essential as it directly impacts product durability and customer satisfaction, which can enhance your brand's reputation. By choosing the right material, you can reduce waste during manufacturing, boost processing efficiency, and ultimately save on long-term costs, even if initial investments seem higher.
It's important to thoroughly evaluate material properties to align with your product priorities, such as performance and aesthetics. Early testing can help you spot potential issues, ensuring product reliability and minimizing customer dissatisfaction. Additionally, considering sustainable practices in your material selection can contribute to a cleaner environment and reduce ecological impact.
Collaborating with material manufacturers can also provide valuable insights, making your selection process smoother and more informed.
Defining Your Product Requirements
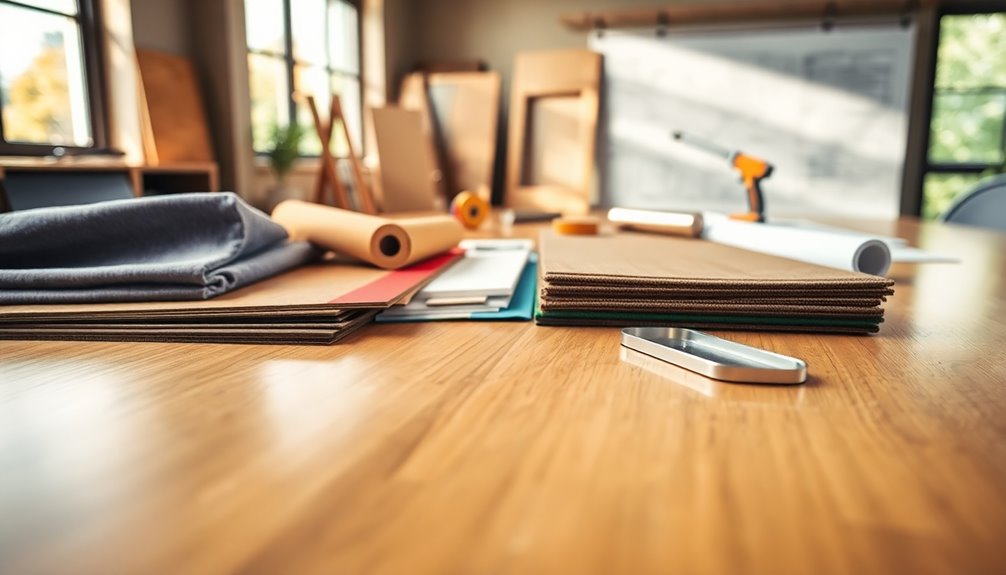
To define your product requirements, start by identifying its purpose; this will streamline your material selection process.
Next, analyze the environmental conditions where it'll be used to guarantee the materials can withstand those factors.
Finally, consider your target audience's preferences, as their needs will shape both the look and functionality of your product. Additionally, understanding the importance of color accuracy can enhance the overall experience of your product.
Identify Product Purpose
How do you guarantee your product meets its intended purpose? Start by understanding its primary purpose, defining your product needs. This clarity shapes your material choices—strength, flexibility, and thermal resistance become vital factors. Consider your target audience; their preferences for aesthetics and functionality should influence your selections. Additionally, ensuring that your product maintains air purification efficiency is crucial for its effectiveness in improving indoor air quality.
Here's a quick reference to help you identify essential properties:
Material Property | Indoor Use | Outdoor Use |
---|---|---|
Durability | Moderate | High |
Weather Resistance | Low | High |
Cost | Low to Moderate | Moderate to High |
Weight | Moderate | Light to Moderate |
Analyze Environmental Conditions
Understanding environmental conditions is essential for defining your product requirements, as these factors directly impact material performance.
When choosing materials, consider temperature fluctuations and humidity levels, as they can greatly influence durability and functionality. For outdoor applications, select materials with weather resistance to protect against UV exposure, moisture, and extreme temperatures.
In high-humidity settings, opt for materials with low water absorption, like certain plastics and metals, to prevent swelling or corrosion. Additionally, assess exposure to chemicals or contaminants to maintain material integrity over time.
Conduct thorough testing under anticipated environmental conditions to validate your material choices and guarantee they meet performance expectations in real-world applications.
Careful analysis will help you find the best materials for your specific needs.
Determine Target Audience
Who exactly is your target audience? Identifying them is essential for defining your product requirements. Understanding their demographics and needs helps you choose materials that meet their expectations. Conducting market research uncovers priorities like sustainability, durability, and aesthetics, guiding your material selection. Feedback from potential users during prototyping can provide insights into their preferences. Tailoring your choices to your target audience boosts acceptance and competitiveness. Additionally, considering factors such as advance directives can help ensure that the materials chosen are not only functional but also aligned with the users' values and needs.
Demographic | Preferences | Material Needs |
---|---|---|
Age Group 18-25 | Eco-friendly options | Sustainable |
Age Group 26-35 | High durability | Robust materials |
Age Group 36-50 | Aesthetic appeal | Stylish finishes |
Age Group 51+ | Comfort and usability | Soft textures |
Professionals | Functionality | Practical solutions |
Evaluating Material Options
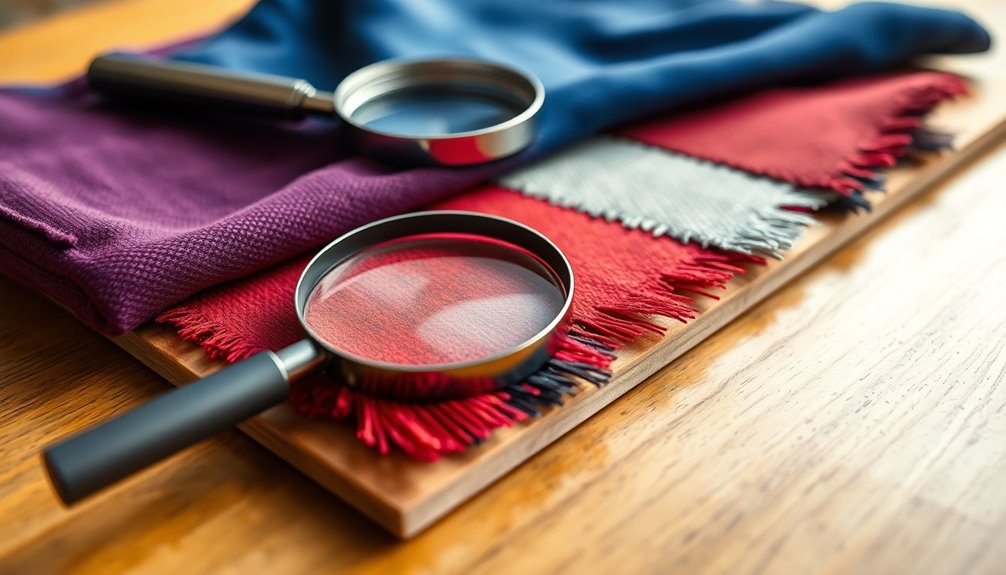
When you're evaluating material options, what factors truly matter for your project?
Start by examining mechanical and chemical properties to guarantee you choose suitable materials that will perform well under specific operating conditions.
Prioritize your options based on performance criteria, cost-effectiveness, and aesthetic appeal, aligning with your product requirements and target audience.
A comparative evaluation of different materials, like metals, plastics, and composites, helps you identify the best fit for your intended application.
Engaging with material suppliers early in the product development process can provide valuable insights on material performance and suitability for manufacturing.
Finally, thorough testing and prototyping are essential for validating your selected materials to guarantee they meet both design and regulatory standards.
Assessing Performance and Durability
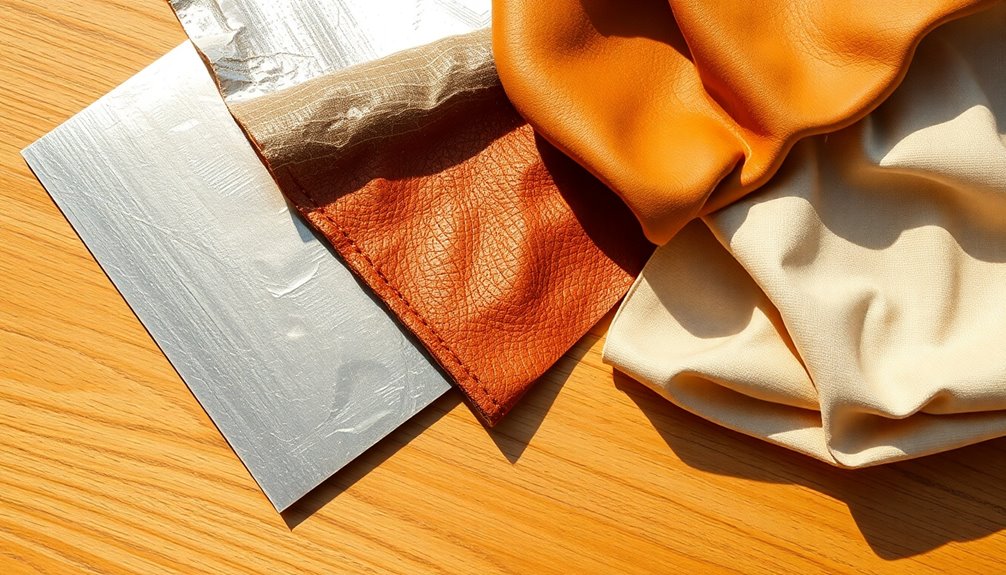
When you're selecting materials, it's essential to evaluate their strength and long-term performance. Consider how different materials hold up under stress and environmental changes, as this can impact your project's success. Testing these factors in real-world scenarios will help you make informed choices that last. Additionally, choosing materials that support sustainable forestry practices can further enhance the environmental benefits of your project.
Material Strength Evaluation
Evaluating material strength is essential for ensuring the performance and durability of products in various applications.
You'll want to assess parameters like tensile, compressive, and yield strength, as these determine how well a material can withstand forces without deforming or failing. Conducting fatigue tests can help reveal a material's lifespan and resistance to wear, while impact resistance tests like Charpy or Izod determine how well it absorbs energy during sudden force applications.
Remember that environmental factors, such as temperature changes and chemical exposure, can affect material performance, so evaluate properties under specific conditions.
Long-term Performance Testing
Long-term performance testing is essential for ensuring that materials hold up under real-world conditions over time. This process evaluates how materials maintain functionality under extended use and varying environmental factors.
Durability assessments often use accelerated aging tests, simulating years of wear and tear in a shorter timeframe, allowing for quicker data collection. You'll want to analyze materials for changes in physical properties like tensile strength and flexibility, as well as resistance to UV exposure and moisture.
Extensive testing also includes real-life application scenarios to identify potential failures before mass production. Engaging independent testing laboratories can provide unbiased results, enhancing your confidence in the long-term reliability of the materials you choose.
Considering Environmental Factors
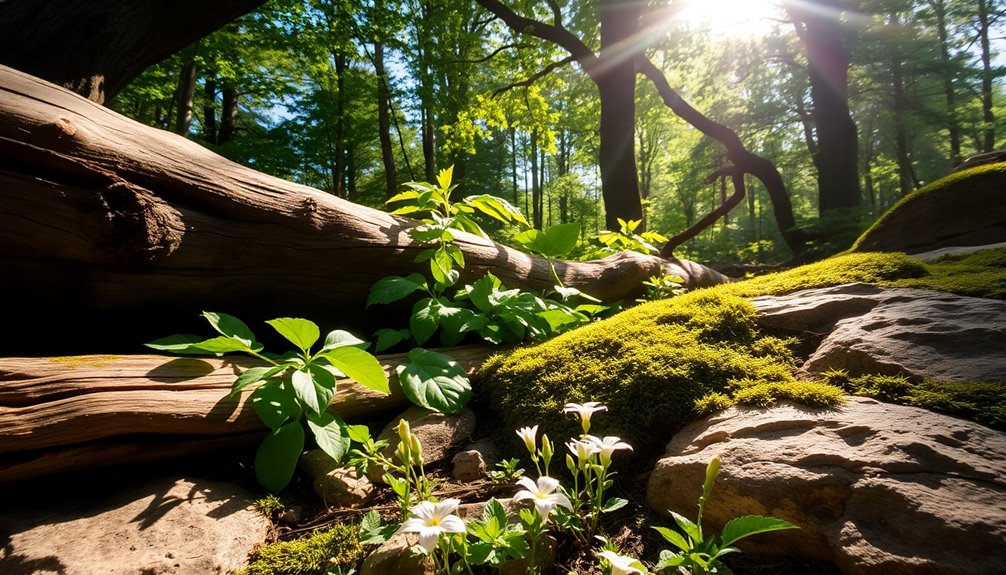
As you consider your material choices, it's vital to recognize how environmental factors can impact their performance. Temperature fluctuations, humidity levels, and UV exposure can greatly affect the longevity and functionality of materials for your product.
If you're designing for outdoor applications, you'll need materials that resist weather-related degradation, like UV-resistant plastics and corrosion-proof metals. Additionally, some adhesives and coatings may fail in extreme temperatures, so selecting materials that withstand specific conditions is imperative.
Keep in mind that material shrinkage or expansion due to temperature and humidity changes can impact tolerances, making stable properties a priority. Conduct a thorough analysis of your intended environment to guarantee your chosen materials meet all performance requirements effectively. Furthermore, considering the refrigeration cycle in your design can enhance energy efficiency, especially in climate-controlled applications.
Tolerance Management in Material Selection
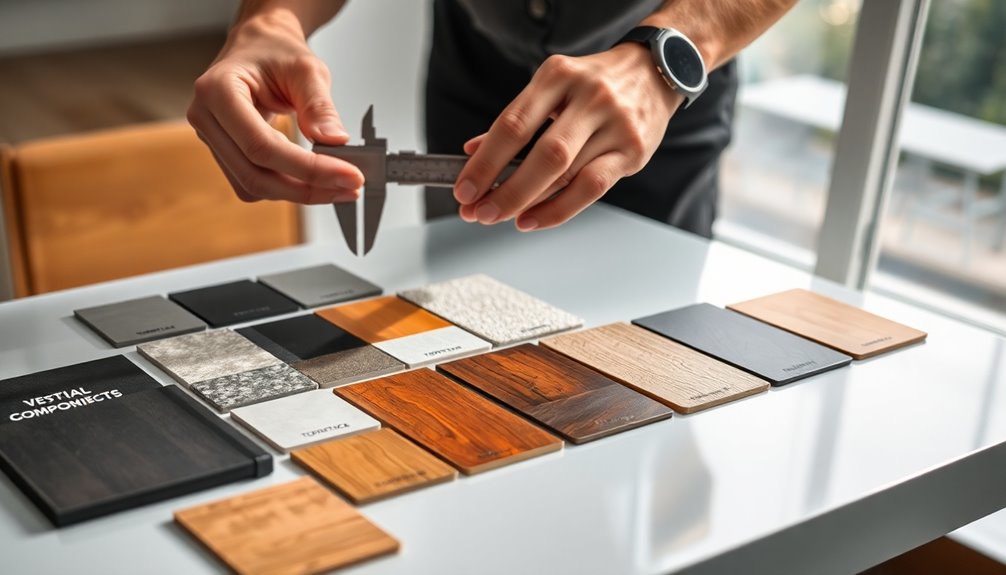
When selecting materials, understanding tolerance levels is essential to guarantee your product meets application needs without inflating manufacturing costs.
By adjusting tolerances appropriately, you can streamline the production process and reduce the risk of defects.
Prioritizing functional tolerances over general ones will enhance your product's performance and reliability.
Importance of Tolerance Levels
Effective tolerance management is vital in material selection, as it determines the acceptable limits for dimensions and features that impact how well components fit together in assemblies. By clearly defining tolerance levels, you can enhance manufacturability and guarantee that parts align with their functional requirements.
Avoid excessively tight tolerances that complicate manufacturing processes, as they often lead to increased costs and longer lead times. Instead, focus on functional tolerances that reflect actual application needs, streamlining operations and reducing waste.
Clear communication between design and manufacturing teams is essential to prevent misunderstandings that could cause costly rework. By utilizing only necessary tolerances, you'll improve overall efficiency and create a more cost-effective production environment.
Impact on Manufacturing Costs
Tolerance management directly influences manufacturing costs, often determining the balance between efficiency and expense. Tighter tolerances increase complexity and can raise costs by 20-30%. You could waste materials and increase scrap rates by being overly precise. Instead, using only the necessary tolerances simplifies processes, potentially reducing costs by 10-15% while maintaining functionality. Effective management can enhance production efficiency, leading to significant savings on labor and materials throughout the product lifecycle.
Tolerance Level | Cost Impact | Waste Potential |
---|---|---|
Loose | Low | Minimal |
Moderate | Moderate | Moderate |
Tight | High | High |
Overly Tight | Very High | Very High |
Necessary Only | Reduced | Minimal |
Adjusting for Application Needs
Managing tolerances not only affects manufacturing costs but also plays an essential role in material selection for specific applications.
By aligning tolerances with application requirements, you can enhance both functionality and efficiency. Here are some key considerations:
- Use only necessary tolerances to simplify manufacturing processes.
- Focus on functional tolerances rather than overly precise specifications.
- Confirm that chosen materials meet the specific performance needs of your application.
- Assess tolerances carefully to improve material choices and manufacturability.
Collaborating With Manufacturing Partners
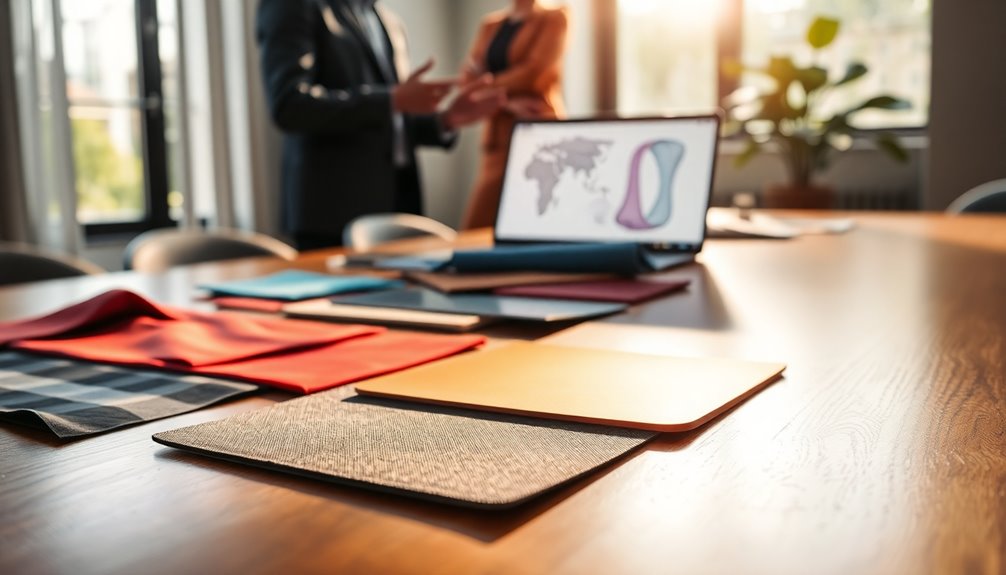
When you collaborate with manufacturing partners early in the material selection process, you reveal valuable insights that can greatly enhance both material performance and cost-effectiveness.
Engaging with these partners gives you access to their expertise, helping you identify the Right Materials for your project. This collaboration streamlines the manufacturing process, allowing you to troubleshoot potential material issues efficiently.
Existing relationships with suppliers can also improve your options and pricing, enabling quicker decisions that reduce overall costs.
By fostering strong partnerships, you create a collaborative environment conducive to innovation in material selection and production techniques.
Ultimately, this proactive approach leads to better product outcomes and a more effective use of resources.
Testing Materials and Prototyping
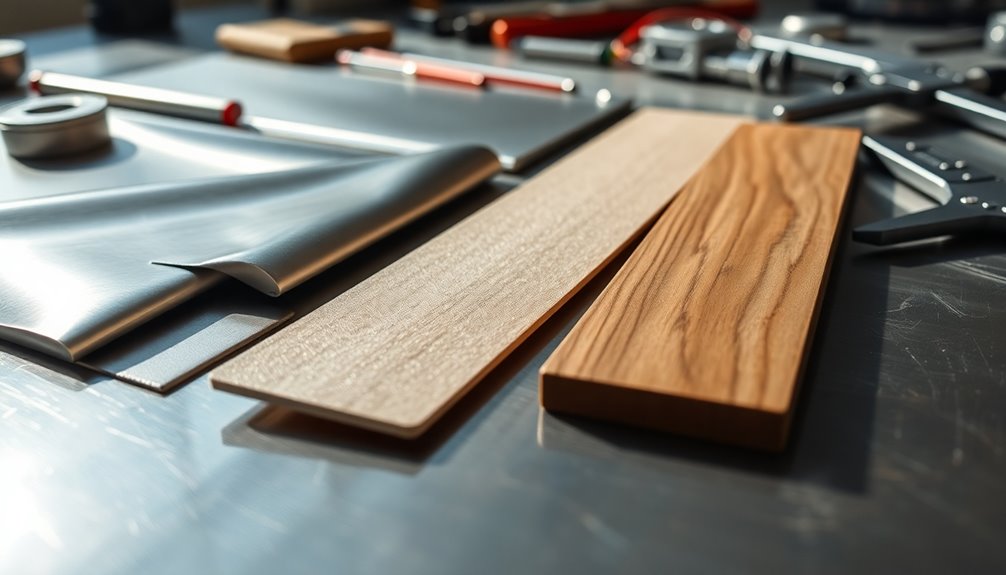
Engaging with manufacturing partners not only streamlines material selection but also sets the stage for effective testing and prototyping.
To guarantee you're making the best choices, consider the following:
- Test materials in their intended shape to reveal performance properties.
- Utilize affordable 3D printing for rapid prototyping, minimizing costs.
- Conduct thorough testing until failure to gather crucial durability data.
- Collaborate with suppliers for test rolls to assess materials before full-scale prototyping.
- Additionally, leveraging user engagement statistics can provide insights into material performance in real-world applications.
Finalizing Material Choices
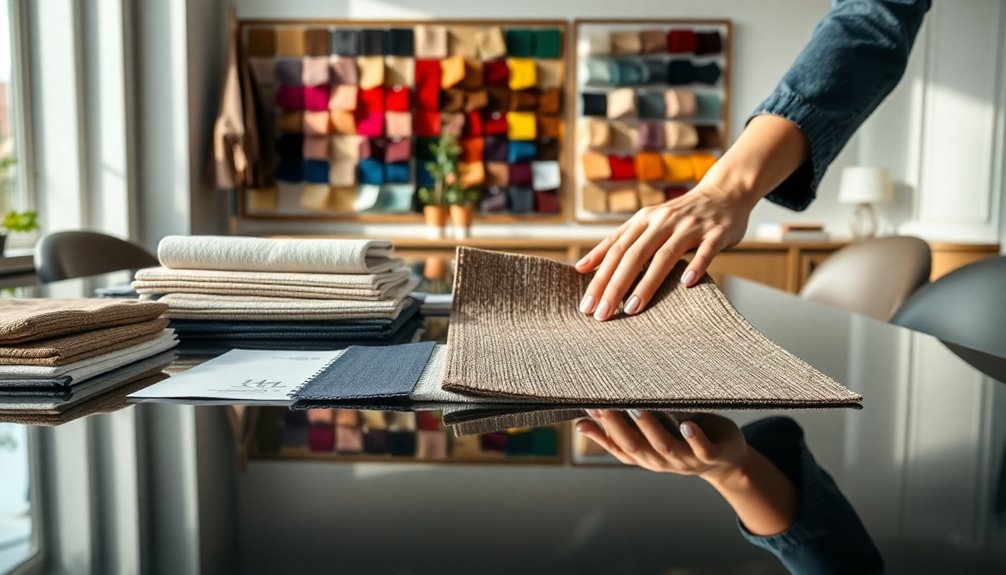
How do you guarantee your material choices are the right fit for your project? Start by thoroughly testing prototypes to confirm they align with your performance, aesthetic, and cost requirements.
When you decide to choose a material, make sure it fits the complexity of your final product.
Once you've selected the materials, update your Bill of Materials (BOM) to reflect your choices and reliable suppliers, streamlining sourcing and production.
It's wise to recommend multiple suppliers for critical components to address potential risks in availability and quality.
Finally, document your findings and evaluations throughout the selection process; this will enhance your decision-making and improve sourcing efficiency for future projects.
Mitigating Risks in Material Selection
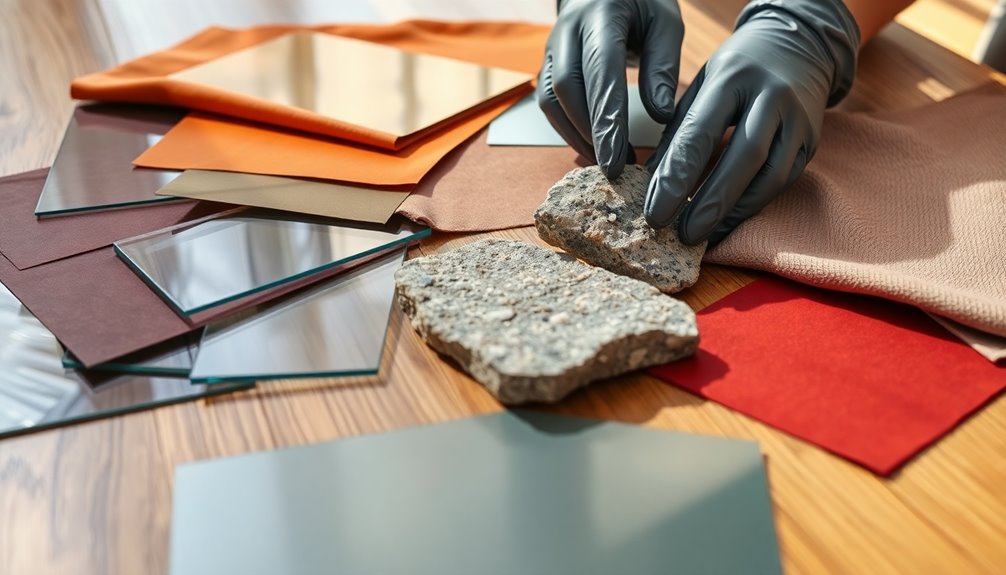
Mitigating risks in material selection is essential for ensuring your project's success, especially since untested materials can lead to costly failures.
To safeguard your project, consider these strategies:
- Conduct thorough testing early to identify potential failures.
- Collaborate with material manufacturers for valuable insights.
- Establish a Bill of Materials (BOM) to spot incompatible components.
- Engage independent testers for unbiased feedback on prototypes. Additionally, utilizing advanced filtration systems can help in selecting materials that contribute to healthier environments.
Frequently Asked Questions
How to Find the Right Material?
To find the right material, start by defining your product's priorities—think about performance, aesthetics, and cost.
Then, gather data through thorough testing of prototypes to see how materials perform in real-life situations.
Engage with suppliers early on to explore options and pricing.
Evaluate materials based on established criteria, environmental factors, and compliance.
Finally, document your findings to guide your decision-making and finalize your Bill of Materials effectively.
What's the Most Useful Material?
When considering the most useful material, think about strength versus weight.
Steel offers incredible durability for structural needs, while lightweight plastics like polypropylene excel in packaging.
Composites, like carbon fiber, provide impressive strength without the bulk, ideal for aerospace.
Wood combines beauty with function, perfect for furniture, yet requires care against moisture.
In medical fields, polycarbonate shines for its safety.
Ultimately, your choice should balance performance and environmental impact.
What Are the 5 Types of Materials and Their Uses?
You've got five main types of materials to evaluate:
Metals, known for strength and durability, are perfect for construction and automotive use.
Plastics, like polypropylene, are lightweight and versatile, ideal for packaging.
Wood offers aesthetic appeal and sustainability in furniture and construction.
Composites combine materials for superior performance in aerospace and sports gear.
Finally, ceramics provide high hardness and thermal stability for everything from tiles to advanced engineering components.
What Are the Three Main Materials?
When you explore the domain of materials, think of metals, plastics, and composites as the three pillars of versatility.
Metals, like steel and aluminum, boast strength and resilience, perfect for building sturdy structures.
Plastics, lightweight and adaptable, charm you with their corrosion resistance, ideal for everyday items.
Meanwhile, composites weave together the best of both worlds, delivering superior performance in demanding fields like aerospace.
Each material shines brightly in its own domain.
Conclusion
In the end, choosing the right materials might seem like a simple task, but you've just uncovered a labyrinth of factors to evaluate. It's ironic, isn't it? What starts as a straightforward decision can morph into a complex puzzle. But remember, taking your time to weigh your options not only guarantees your product shines but also saves you from costly mistakes down the line. So, embrace the process; after all, it's just a matter of picking the best for your needs.